A mental material--Industrial pure iron
Introduction:
Industrial pure iron is a type of steel, whose chemical composition is mainly iron, with a content ranging from 99.50% to 99.90% and a carbon content below 0.04%. The fewer other elements, the better.
Features:
Generally, industrial pure iron is particularly soft, has great toughness, and excellent electromagnetic performance.
Use:
Industrial pure iron is an important raw material used for smelting precision alloys, high-temperature alloys, ultra-low carbon stainless steel, electric heating alloys, and other materials. There are two common specifications. One is used as a deep drawing material, which can be stamped into extremely complex shapes; Another type is used as electromagnetic materials with high magnetic susceptibility and low diamagnetism.
Several common grades of steel
1. Q235: This type of steel is widely used in construction and bridge structures.
2.16Mn: This is a high-strength low alloy structural steel widely used in the manufacturing of bridges, ships, automobiles, houses, pressure vessels, and other industries.
3.Y30:The mechanical properties are relatively high, and the machinability is also appropriately improved, which can manufacture standard parts with high strength requirements.
4.Y40Mn:High quality carbon structural steel is widely used in the manufacturing of important mechanical parts due to its excellent hardness and wear resistance.
5.YF40MnV:High strength and high toughness steel, with excellent processing and welding performance.
6.08#:High quality low-carbon steel, this material has excellent plasticity and toughness, as well as good welding performance and cold and hot processing performance.
7.15#:It has good comprehensive performance, moderate price, and is widely used in various fields.
8.35#:High quality carbon structural steel. It has good hardness and strength, and is therefore widely used in the manufacturing of various important mechanical parts.
9.45#: used in precision mechanical manufacturing.
A plastic material--Polyethylene(PE)
Introduction:
Polyethylene (PE) is a thermoplastic resin produced by polymerization of ethylene monomers. In industry, it also includes copolymers of ethylene and small amounts of alpha olefins.
Features:
Polyethylene resin is a non-toxic and odorless white powder or particle with a milky white appearance and a waxy texture. It has a low water absorption rate of less than 0.01%. The polyethylene film is transparent and decreases with increasing crystallinity. Polyethylene film has a low water permeability but high air permeability, making it unsuitable for fresh-keeping packaging and suitable for moisture-proof packaging. Flammable, with an oxygen index of 17.4, low smoke during combustion, with a small amount of molten droplets, yellow on top and blue on the flame, and a smell of paraffin. Polyethylene has good water resistance. The surface of the product is non-polar, making it difficult to bond and print, and has been improved through surface treatment. Multiple branched chains result in poor resistance to photodegradation and oxidation.
Use :
Polyethylene is highly sensitive to environmental stress (chemical and mechanical effects) and can be processed using general thermoplastic molding methods. Polyethylene has a wide range of applications, mainly used to manufacture films, packaging materials, containers, pipelines, monofilaments, wires and cables, daily necessities, etc. It can also be used as a high-frequency insulation material for televisions, radars, etc.
A composite material--FRP
Introduction:
Fiberglass reinforced plastic (FRP), also known as fiberglass reinforced plastic (FRP), generally refers to reinforced plastics made of glass fiber reinforced unsaturated polyester, epoxy resin, and phenolic resin matrix, with glass fiber or its products as reinforcing materials. It is called fiberglass reinforced plastic, or fiberglass reinforced plastic, which is different from tempered glass.
Features:
Lightweight and high-strength Corrosion resistanceGood electrical performance Good thermal performance Good designability Low elastic modulusPoor long-term temperature resistance Aging phenomenon Low shear strength
Use:
1. Construction industry: cooling towers, fiberglass building structures, indoor equipment and decorations, decorative panels, saunas, concrete formwork, reinforcement materials, and solar energy utilization devices. 2. Chemical industry: corrosion-resistant conveying pumps and their accessories, corrosion-resistant valves, ventilation facilities, wastewater treatment equipment, etc. 3. The automotive and railway transportation industry: automotive casings and other components, all plastic micro cars, bumpers, instrument screens, small passenger and freight vehicles, as well as cab and machine covers for fire tanker trucks, refrigerated trucks, tractors, etc. 4. In terms of railway transportation, there are train window frames, curved roof panels, roof water tanks, water storage tanks, and certain railway communication facilities. 5. In terms of highway construction, there are traffic signs, isolation piers, signs, highway guardrails, and so on. 6. Inland passenger and cargo ships, fishing boats, hovercraft, high-speed boats, lifeboats, as well as fiberglass buoy drums and mooring buoys. 7. Electrical industry and communication engineering: including arc extinguishing equipment, cable protection tubes, generator stator coils and support rings and conical shells, insulation tubes, insulation rods, motor protection rings, etc
Link
Learn 2 new material
Features:
Generally, industrial pure iron is particularly soft, has great toughness, and excellent electromagnetic performance.
Use:
Industrial pure iron is an important raw material used for smelting precision alloys, high-temperature alloys, ultra-low carbon stainless steel, electric heating alloys, and other materials. There are two common specifications. One is used as a deep drawing material, which can be stamped into extremely complex shapes; Another type is used as electromagnetic materials with high magnetic susceptibility and low diamagnetism.
Several common grades of steel
1. Q235: This type of steel is widely used in construction and bridge structures.
2.16Mn: This is a high-strength low alloy structural steel widely used in the manufacturing of bridges, ships, automobiles, houses, pressure vessels, and other industries.
3.Y30:The mechanical properties are relatively high, and the machinability is also appropriately improved, which can manufacture standard parts with high strength requirements.
4.Y40Mn:High quality carbon structural steel is widely used in the manufacturing of important mechanical parts due to its excellent hardness and wear resistance.
5.YF40MnV:High strength and high toughness steel, with excellent processing and welding performance.
6.08#:High quality low-carbon steel, this material has excellent plasticity and toughness, as well as good welding performance and cold and hot processing performance.
7.15#:It has good comprehensive performance, moderate price, and is widely used in various fields.
8.35#:High quality carbon structural steel. It has good hardness and strength, and is therefore widely used in the manufacturing of various important mechanical parts.
9.45#: used in precision mechanical manufacturing.
A plastic material--Polyethylene(PE)
Introduction:
Polyethylene (PE) is a thermoplastic resin produced by polymerization of ethylene monomers. In industry, it also includes copolymers of ethylene and small amounts of alpha olefins.
Features:
Polyethylene resin is a non-toxic and odorless white powder or particle with a milky white appearance and a waxy texture. It has a low water absorption rate of less than 0.01%. The polyethylene film is transparent and decreases with increasing crystallinity. Polyethylene film has a low water permeability but high air permeability, making it unsuitable for fresh-keeping packaging and suitable for moisture-proof packaging. Flammable, with an oxygen index of 17.4, low smoke during combustion, with a small amount of molten droplets, yellow on top and blue on the flame, and a smell of paraffin. Polyethylene has good water resistance. The surface of the product is non-polar, making it difficult to bond and print, and has been improved through surface treatment. Multiple branched chains result in poor resistance to photodegradation and oxidation.
Use :
Polyethylene is highly sensitive to environmental stress (chemical and mechanical effects) and can be processed using general thermoplastic molding methods. Polyethylene has a wide range of applications, mainly used to manufacture films, packaging materials, containers, pipelines, monofilaments, wires and cables, daily necessities, etc. It can also be used as a high-frequency insulation material for televisions, radars, etc.
A composite material--FRP
Introduction:
Fiberglass reinforced plastic (FRP), also known as fiberglass reinforced plastic (FRP), generally refers to reinforced plastics made of glass fiber reinforced unsaturated polyester, epoxy resin, and phenolic resin matrix, with glass fiber or its products as reinforcing materials. It is called fiberglass reinforced plastic, or fiberglass reinforced plastic, which is different from tempered glass.
Features:
Lightweight and high-strength Corrosion resistanceGood electrical performance Good thermal performance Good designability Low elastic modulusPoor long-term temperature resistance Aging phenomenon Low shear strength
Use:
1. Construction industry: cooling towers, fiberglass building structures, indoor equipment and decorations, decorative panels, saunas, concrete formwork, reinforcement materials, and solar energy utilization devices. 2. Chemical industry: corrosion-resistant conveying pumps and their accessories, corrosion-resistant valves, ventilation facilities, wastewater treatment equipment, etc. 3. The automotive and railway transportation industry: automotive casings and other components, all plastic micro cars, bumpers, instrument screens, small passenger and freight vehicles, as well as cab and machine covers for fire tanker trucks, refrigerated trucks, tractors, etc. 4. In terms of railway transportation, there are train window frames, curved roof panels, roof water tanks, water storage tanks, and certain railway communication facilities. 5. In terms of highway construction, there are traffic signs, isolation piers, signs, highway guardrails, and so on. 6. Inland passenger and cargo ships, fishing boats, hovercraft, high-speed boats, lifeboats, as well as fiberglass buoy drums and mooring buoys. 7. Electrical industry and communication engineering: including arc extinguishing equipment, cable protection tubes, generator stator coils and support rings and conical shells, insulation tubes, insulation rods, motor protection rings, etc
Link
Learn 2 new material

Several common grades of steel

1. Q235: This type of steel is widely used in construction and bridge structures.
2.16Mn: This is a high-strength low alloy structural steel widely used in the manufacturing of bridges, ships, automobiles, houses, pressure vessels, and other industries.
3.Y30:The mechanical properties are relatively high, and the machinability is also appropriately improved, which can manufacture standard parts with high strength requirements.
4.Y40Mn:High quality carbon structural steel is widely used in the manufacturing of important mechanical parts due to its excellent hardness and wear resistance.
5.YF40MnV:High strength and high toughness steel, with excellent processing and welding performance.
6.08#:High quality low-carbon steel, this material has excellent plasticity and toughness, as well as good welding performance and cold and hot processing performance.
7.15#:It has good comprehensive performance, moderate price, and is widely used in various fields.
8.35#:High quality carbon structural steel. It has good hardness and strength, and is therefore widely used in the manufacturing of various important mechanical parts.
9.45#: used in precision mechanical manufacturing.
A plastic material--Polyethylene(PE)
Introduction:
Polyethylene (PE) is a thermoplastic resin produced by polymerization of ethylene monomers. In industry, it also includes copolymers of ethylene and small amounts of alpha olefins.
Features:
Polyethylene resin is a non-toxic and odorless white powder or particle with a milky white appearance and a waxy texture. It has a low water absorption rate of less than 0.01%. The polyethylene film is transparent and decreases with increasing crystallinity. Polyethylene film has a low water permeability but high air permeability, making it unsuitable for fresh-keeping packaging and suitable for moisture-proof packaging. Flammable, with an oxygen index of 17.4, low smoke during combustion, with a small amount of molten droplets, yellow on top and blue on the flame, and a smell of paraffin. Polyethylene has good water resistance. The surface of the product is non-polar, making it difficult to bond and print, and has been improved through surface treatment. Multiple branched chains result in poor resistance to photodegradation and oxidation.
Use :
Polyethylene is highly sensitive to environmental stress (chemical and mechanical effects) and can be processed using general thermoplastic molding methods. Polyethylene has a wide range of applications, mainly used to manufacture films, packaging materials, containers, pipelines, monofilaments, wires and cables, daily necessities, etc. It can also be used as a high-frequency insulation material for televisions, radars, etc.
A composite material--FRP
Introduction:
Fiberglass reinforced plastic (FRP), also known as fiberglass reinforced plastic (FRP), generally refers to reinforced plastics made of glass fiber reinforced unsaturated polyester, epoxy resin, and phenolic resin matrix, with glass fiber or its products as reinforcing materials. It is called fiberglass reinforced plastic, or fiberglass reinforced plastic, which is different from tempered glass.
Features:
Lightweight and high-strength Corrosion resistanceGood electrical performance Good thermal performance Good designability Low elastic modulusPoor long-term temperature resistance Aging phenomenon Low shear strength
Use:
1. Construction industry: cooling towers, fiberglass building structures, indoor equipment and decorations, decorative panels, saunas, concrete formwork, reinforcement materials, and solar energy utilization devices. 2. Chemical industry: corrosion-resistant conveying pumps and their accessories, corrosion-resistant valves, ventilation facilities, wastewater treatment equipment, etc. 3. The automotive and railway transportation industry: automotive casings and other components, all plastic micro cars, bumpers, instrument screens, small passenger and freight vehicles, as well as cab and machine covers for fire tanker trucks, refrigerated trucks, tractors, etc. 4. In terms of railway transportation, there are train window frames, curved roof panels, roof water tanks, water storage tanks, and certain railway communication facilities. 5. In terms of highway construction, there are traffic signs, isolation piers, signs, highway guardrails, and so on. 6. Inland passenger and cargo ships, fishing boats, hovercraft, high-speed boats, lifeboats, as well as fiberglass buoy drums and mooring buoys. 7. Electrical industry and communication engineering: including arc extinguishing equipment, cable protection tubes, generator stator coils and support rings and conical shells, insulation tubes, insulation rods, motor protection rings, etc
Link
Learn 2 new material
3.Y30:The mechanical properties are relatively high, and the machinability is also appropriately improved, which can manufacture standard parts with high strength requirements.
4.Y40Mn:High quality carbon structural steel is widely used in the manufacturing of important mechanical parts due to its excellent hardness and wear resistance.
5.YF40MnV:High strength and high toughness steel, with excellent processing and welding performance.
6.08#:High quality low-carbon steel, this material has excellent plasticity and toughness, as well as good welding performance and cold and hot processing performance.
7.15#:It has good comprehensive performance, moderate price, and is widely used in various fields.
8.35#:High quality carbon structural steel. It has good hardness and strength, and is therefore widely used in the manufacturing of various important mechanical parts.
9.45#: used in precision mechanical manufacturing.
A plastic material--Polyethylene(PE)
Introduction:
Polyethylene (PE) is a thermoplastic resin produced by polymerization of ethylene monomers. In industry, it also includes copolymers of ethylene and small amounts of alpha olefins.
Features:
Polyethylene resin is a non-toxic and odorless white powder or particle with a milky white appearance and a waxy texture. It has a low water absorption rate of less than 0.01%. The polyethylene film is transparent and decreases with increasing crystallinity. Polyethylene film has a low water permeability but high air permeability, making it unsuitable for fresh-keeping packaging and suitable for moisture-proof packaging. Flammable, with an oxygen index of 17.4, low smoke during combustion, with a small amount of molten droplets, yellow on top and blue on the flame, and a smell of paraffin. Polyethylene has good water resistance. The surface of the product is non-polar, making it difficult to bond and print, and has been improved through surface treatment. Multiple branched chains result in poor resistance to photodegradation and oxidation.
Use :
Polyethylene is highly sensitive to environmental stress (chemical and mechanical effects) and can be processed using general thermoplastic molding methods. Polyethylene has a wide range of applications, mainly used to manufacture films, packaging materials, containers, pipelines, monofilaments, wires and cables, daily necessities, etc. It can also be used as a high-frequency insulation material for televisions, radars, etc.
A composite material--FRP
Introduction:
Fiberglass reinforced plastic (FRP), also known as fiberglass reinforced plastic (FRP), generally refers to reinforced plastics made of glass fiber reinforced unsaturated polyester, epoxy resin, and phenolic resin matrix, with glass fiber or its products as reinforcing materials. It is called fiberglass reinforced plastic, or fiberglass reinforced plastic, which is different from tempered glass.
Features:
Lightweight and high-strength Corrosion resistanceGood electrical performance Good thermal performance Good designability Low elastic modulusPoor long-term temperature resistance Aging phenomenon Low shear strength
Use:
1. Construction industry: cooling towers, fiberglass building structures, indoor equipment and decorations, decorative panels, saunas, concrete formwork, reinforcement materials, and solar energy utilization devices. 2. Chemical industry: corrosion-resistant conveying pumps and their accessories, corrosion-resistant valves, ventilation facilities, wastewater treatment equipment, etc. 3. The automotive and railway transportation industry: automotive casings and other components, all plastic micro cars, bumpers, instrument screens, small passenger and freight vehicles, as well as cab and machine covers for fire tanker trucks, refrigerated trucks, tractors, etc. 4. In terms of railway transportation, there are train window frames, curved roof panels, roof water tanks, water storage tanks, and certain railway communication facilities. 5. In terms of highway construction, there are traffic signs, isolation piers, signs, highway guardrails, and so on. 6. Inland passenger and cargo ships, fishing boats, hovercraft, high-speed boats, lifeboats, as well as fiberglass buoy drums and mooring buoys. 7. Electrical industry and communication engineering: including arc extinguishing equipment, cable protection tubes, generator stator coils and support rings and conical shells, insulation tubes, insulation rods, motor protection rings, etc
Link
Learn 2 new material
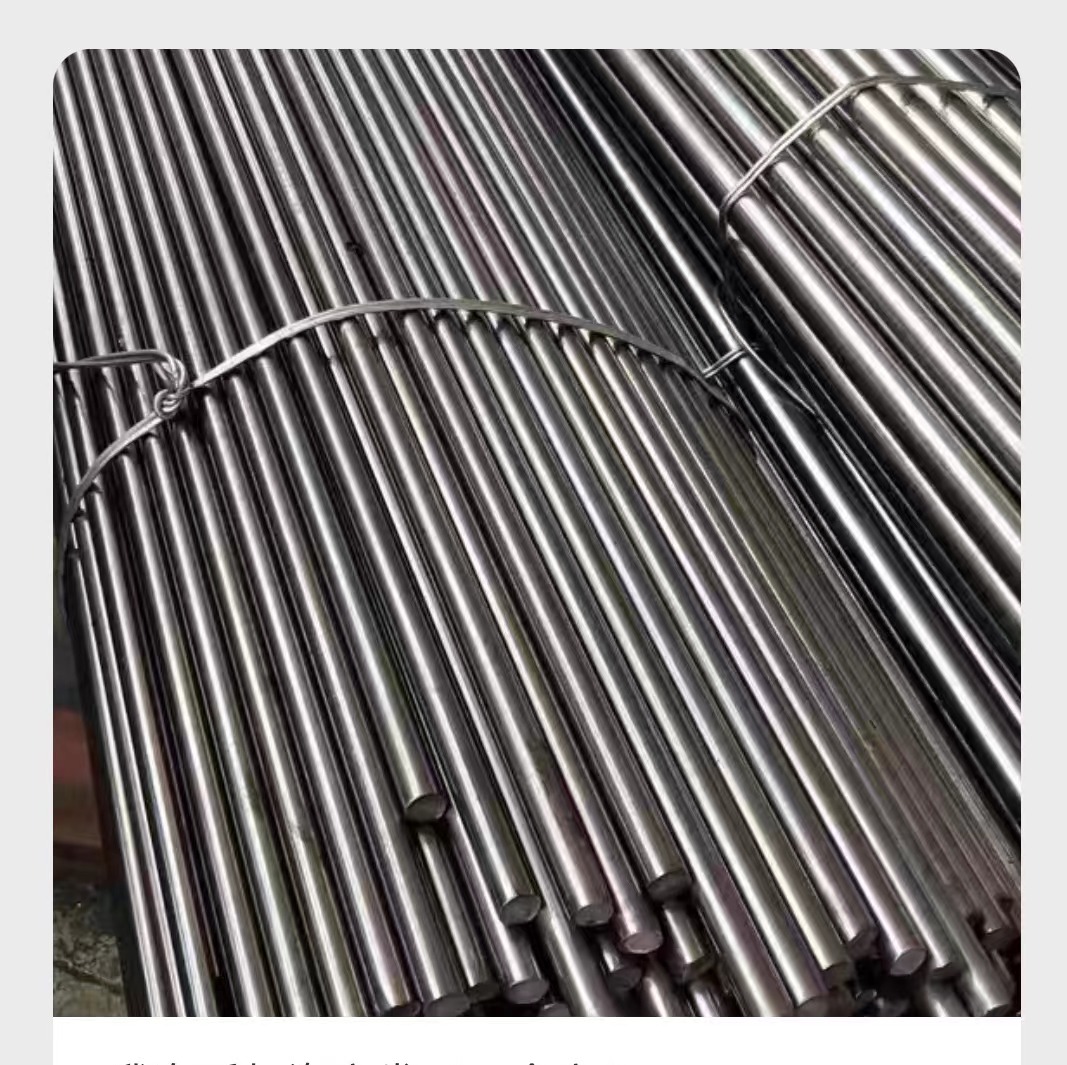
5.YF40MnV:High strength and high toughness steel, with excellent processing and welding performance.
6.08#:High quality low-carbon steel, this material has excellent plasticity and toughness, as well as good welding performance and cold and hot processing performance.
7.15#:It has good comprehensive performance, moderate price, and is widely used in various fields.
8.35#:High quality carbon structural steel. It has good hardness and strength, and is therefore widely used in the manufacturing of various important mechanical parts.
9.45#: used in precision mechanical manufacturing.
A plastic material--Polyethylene(PE)
Introduction:
Polyethylene (PE) is a thermoplastic resin produced by polymerization of ethylene monomers. In industry, it also includes copolymers of ethylene and small amounts of alpha olefins.
Features:
Polyethylene resin is a non-toxic and odorless white powder or particle with a milky white appearance and a waxy texture. It has a low water absorption rate of less than 0.01%. The polyethylene film is transparent and decreases with increasing crystallinity. Polyethylene film has a low water permeability but high air permeability, making it unsuitable for fresh-keeping packaging and suitable for moisture-proof packaging. Flammable, with an oxygen index of 17.4, low smoke during combustion, with a small amount of molten droplets, yellow on top and blue on the flame, and a smell of paraffin. Polyethylene has good water resistance. The surface of the product is non-polar, making it difficult to bond and print, and has been improved through surface treatment. Multiple branched chains result in poor resistance to photodegradation and oxidation.
Use :
Polyethylene is highly sensitive to environmental stress (chemical and mechanical effects) and can be processed using general thermoplastic molding methods. Polyethylene has a wide range of applications, mainly used to manufacture films, packaging materials, containers, pipelines, monofilaments, wires and cables, daily necessities, etc. It can also be used as a high-frequency insulation material for televisions, radars, etc.
A composite material--FRP
Introduction:
Fiberglass reinforced plastic (FRP), also known as fiberglass reinforced plastic (FRP), generally refers to reinforced plastics made of glass fiber reinforced unsaturated polyester, epoxy resin, and phenolic resin matrix, with glass fiber or its products as reinforcing materials. It is called fiberglass reinforced plastic, or fiberglass reinforced plastic, which is different from tempered glass.
Features:
Lightweight and high-strength Corrosion resistanceGood electrical performance Good thermal performance Good designability Low elastic modulusPoor long-term temperature resistance Aging phenomenon Low shear strength
Use:
1. Construction industry: cooling towers, fiberglass building structures, indoor equipment and decorations, decorative panels, saunas, concrete formwork, reinforcement materials, and solar energy utilization devices. 2. Chemical industry: corrosion-resistant conveying pumps and their accessories, corrosion-resistant valves, ventilation facilities, wastewater treatment equipment, etc. 3. The automotive and railway transportation industry: automotive casings and other components, all plastic micro cars, bumpers, instrument screens, small passenger and freight vehicles, as well as cab and machine covers for fire tanker trucks, refrigerated trucks, tractors, etc. 4. In terms of railway transportation, there are train window frames, curved roof panels, roof water tanks, water storage tanks, and certain railway communication facilities. 5. In terms of highway construction, there are traffic signs, isolation piers, signs, highway guardrails, and so on. 6. Inland passenger and cargo ships, fishing boats, hovercraft, high-speed boats, lifeboats, as well as fiberglass buoy drums and mooring buoys. 7. Electrical industry and communication engineering: including arc extinguishing equipment, cable protection tubes, generator stator coils and support rings and conical shells, insulation tubes, insulation rods, motor protection rings, etc
Link
Learn 2 new material
7.15#:It has good comprehensive performance, moderate price, and is widely used in various fields.
8.35#:High quality carbon structural steel. It has good hardness and strength, and is therefore widely used in the manufacturing of various important mechanical parts.
9.45#: used in precision mechanical manufacturing.
A plastic material--Polyethylene(PE)
Introduction:
Polyethylene (PE) is a thermoplastic resin produced by polymerization of ethylene monomers. In industry, it also includes copolymers of ethylene and small amounts of alpha olefins.
Features:
Polyethylene resin is a non-toxic and odorless white powder or particle with a milky white appearance and a waxy texture. It has a low water absorption rate of less than 0.01%. The polyethylene film is transparent and decreases with increasing crystallinity. Polyethylene film has a low water permeability but high air permeability, making it unsuitable for fresh-keeping packaging and suitable for moisture-proof packaging. Flammable, with an oxygen index of 17.4, low smoke during combustion, with a small amount of molten droplets, yellow on top and blue on the flame, and a smell of paraffin. Polyethylene has good water resistance. The surface of the product is non-polar, making it difficult to bond and print, and has been improved through surface treatment. Multiple branched chains result in poor resistance to photodegradation and oxidation.
Use :
Polyethylene is highly sensitive to environmental stress (chemical and mechanical effects) and can be processed using general thermoplastic molding methods. Polyethylene has a wide range of applications, mainly used to manufacture films, packaging materials, containers, pipelines, monofilaments, wires and cables, daily necessities, etc. It can also be used as a high-frequency insulation material for televisions, radars, etc.
A composite material--FRP
Introduction:
Fiberglass reinforced plastic (FRP), also known as fiberglass reinforced plastic (FRP), generally refers to reinforced plastics made of glass fiber reinforced unsaturated polyester, epoxy resin, and phenolic resin matrix, with glass fiber or its products as reinforcing materials. It is called fiberglass reinforced plastic, or fiberglass reinforced plastic, which is different from tempered glass.
Features:
Lightweight and high-strength Corrosion resistanceGood electrical performance Good thermal performance Good designability Low elastic modulusPoor long-term temperature resistance Aging phenomenon Low shear strength
Use:
1. Construction industry: cooling towers, fiberglass building structures, indoor equipment and decorations, decorative panels, saunas, concrete formwork, reinforcement materials, and solar energy utilization devices. 2. Chemical industry: corrosion-resistant conveying pumps and their accessories, corrosion-resistant valves, ventilation facilities, wastewater treatment equipment, etc. 3. The automotive and railway transportation industry: automotive casings and other components, all plastic micro cars, bumpers, instrument screens, small passenger and freight vehicles, as well as cab and machine covers for fire tanker trucks, refrigerated trucks, tractors, etc. 4. In terms of railway transportation, there are train window frames, curved roof panels, roof water tanks, water storage tanks, and certain railway communication facilities. 5. In terms of highway construction, there are traffic signs, isolation piers, signs, highway guardrails, and so on. 6. Inland passenger and cargo ships, fishing boats, hovercraft, high-speed boats, lifeboats, as well as fiberglass buoy drums and mooring buoys. 7. Electrical industry and communication engineering: including arc extinguishing equipment, cable protection tubes, generator stator coils and support rings and conical shells, insulation tubes, insulation rods, motor protection rings, etc
Link
Learn 2 new material
9.45#: used in precision mechanical manufacturing.
A plastic material--Polyethylene(PE)
Introduction:
Polyethylene (PE) is a thermoplastic resin produced by polymerization of ethylene monomers. In industry, it also includes copolymers of ethylene and small amounts of alpha olefins.
Features:
Polyethylene resin is a non-toxic and odorless white powder or particle with a milky white appearance and a waxy texture. It has a low water absorption rate of less than 0.01%. The polyethylene film is transparent and decreases with increasing crystallinity. Polyethylene film has a low water permeability but high air permeability, making it unsuitable for fresh-keeping packaging and suitable for moisture-proof packaging. Flammable, with an oxygen index of 17.4, low smoke during combustion, with a small amount of molten droplets, yellow on top and blue on the flame, and a smell of paraffin. Polyethylene has good water resistance. The surface of the product is non-polar, making it difficult to bond and print, and has been improved through surface treatment. Multiple branched chains result in poor resistance to photodegradation and oxidation.
Use :
Polyethylene is highly sensitive to environmental stress (chemical and mechanical effects) and can be processed using general thermoplastic molding methods. Polyethylene has a wide range of applications, mainly used to manufacture films, packaging materials, containers, pipelines, monofilaments, wires and cables, daily necessities, etc. It can also be used as a high-frequency insulation material for televisions, radars, etc.
A composite material--FRP
Introduction:
Fiberglass reinforced plastic (FRP), also known as fiberglass reinforced plastic (FRP), generally refers to reinforced plastics made of glass fiber reinforced unsaturated polyester, epoxy resin, and phenolic resin matrix, with glass fiber or its products as reinforcing materials. It is called fiberglass reinforced plastic, or fiberglass reinforced plastic, which is different from tempered glass.
Features:
Lightweight and high-strength Corrosion resistanceGood electrical performance Good thermal performance Good designability Low elastic modulusPoor long-term temperature resistance Aging phenomenon Low shear strength
Use:
1. Construction industry: cooling towers, fiberglass building structures, indoor equipment and decorations, decorative panels, saunas, concrete formwork, reinforcement materials, and solar energy utilization devices. 2. Chemical industry: corrosion-resistant conveying pumps and their accessories, corrosion-resistant valves, ventilation facilities, wastewater treatment equipment, etc. 3. The automotive and railway transportation industry: automotive casings and other components, all plastic micro cars, bumpers, instrument screens, small passenger and freight vehicles, as well as cab and machine covers for fire tanker trucks, refrigerated trucks, tractors, etc. 4. In terms of railway transportation, there are train window frames, curved roof panels, roof water tanks, water storage tanks, and certain railway communication facilities. 5. In terms of highway construction, there are traffic signs, isolation piers, signs, highway guardrails, and so on. 6. Inland passenger and cargo ships, fishing boats, hovercraft, high-speed boats, lifeboats, as well as fiberglass buoy drums and mooring buoys. 7. Electrical industry and communication engineering: including arc extinguishing equipment, cable protection tubes, generator stator coils and support rings and conical shells, insulation tubes, insulation rods, motor protection rings, etc
Link
Learn 2 new material
Polyethylene (PE) is a thermoplastic resin produced by polymerization of ethylene monomers. In industry, it also includes copolymers of ethylene and small amounts of alpha olefins.
Features:
Polyethylene resin is a non-toxic and odorless white powder or particle with a milky white appearance and a waxy texture. It has a low water absorption rate of less than 0.01%. The polyethylene film is transparent and decreases with increasing crystallinity. Polyethylene film has a low water permeability but high air permeability, making it unsuitable for fresh-keeping packaging and suitable for moisture-proof packaging. Flammable, with an oxygen index of 17.4, low smoke during combustion, with a small amount of molten droplets, yellow on top and blue on the flame, and a smell of paraffin. Polyethylene has good water resistance. The surface of the product is non-polar, making it difficult to bond and print, and has been improved through surface treatment. Multiple branched chains result in poor resistance to photodegradation and oxidation.
Use :
Polyethylene is highly sensitive to environmental stress (chemical and mechanical effects) and can be processed using general thermoplastic molding methods. Polyethylene has a wide range of applications, mainly used to manufacture films, packaging materials, containers, pipelines, monofilaments, wires and cables, daily necessities, etc. It can also be used as a high-frequency insulation material for televisions, radars, etc.
A composite material--FRP
Introduction:
Fiberglass reinforced plastic (FRP), also known as fiberglass reinforced plastic (FRP), generally refers to reinforced plastics made of glass fiber reinforced unsaturated polyester, epoxy resin, and phenolic resin matrix, with glass fiber or its products as reinforcing materials. It is called fiberglass reinforced plastic, or fiberglass reinforced plastic, which is different from tempered glass.
Features:
Lightweight and high-strength Corrosion resistanceGood electrical performance Good thermal performance Good designability Low elastic modulusPoor long-term temperature resistance Aging phenomenon Low shear strength
Use:
1. Construction industry: cooling towers, fiberglass building structures, indoor equipment and decorations, decorative panels, saunas, concrete formwork, reinforcement materials, and solar energy utilization devices. 2. Chemical industry: corrosion-resistant conveying pumps and their accessories, corrosion-resistant valves, ventilation facilities, wastewater treatment equipment, etc. 3. The automotive and railway transportation industry: automotive casings and other components, all plastic micro cars, bumpers, instrument screens, small passenger and freight vehicles, as well as cab and machine covers for fire tanker trucks, refrigerated trucks, tractors, etc. 4. In terms of railway transportation, there are train window frames, curved roof panels, roof water tanks, water storage tanks, and certain railway communication facilities. 5. In terms of highway construction, there are traffic signs, isolation piers, signs, highway guardrails, and so on. 6. Inland passenger and cargo ships, fishing boats, hovercraft, high-speed boats, lifeboats, as well as fiberglass buoy drums and mooring buoys. 7. Electrical industry and communication engineering: including arc extinguishing equipment, cable protection tubes, generator stator coils and support rings and conical shells, insulation tubes, insulation rods, motor protection rings, etc
Link
Learn 2 new material
Fiberglass reinforced plastic (FRP), also known as fiberglass reinforced plastic (FRP), generally refers to reinforced plastics made of glass fiber reinforced unsaturated polyester, epoxy resin, and phenolic resin matrix, with glass fiber or its products as reinforcing materials. It is called fiberglass reinforced plastic, or fiberglass reinforced plastic, which is different from tempered glass.
Features:
Lightweight and high-strength Corrosion resistanceGood electrical performance Good thermal performance Good designability Low elastic modulusPoor long-term temperature resistance Aging phenomenon Low shear strength
Use:
1. Construction industry: cooling towers, fiberglass building structures, indoor equipment and decorations, decorative panels, saunas, concrete formwork, reinforcement materials, and solar energy utilization devices. 2. Chemical industry: corrosion-resistant conveying pumps and their accessories, corrosion-resistant valves, ventilation facilities, wastewater treatment equipment, etc. 3. The automotive and railway transportation industry: automotive casings and other components, all plastic micro cars, bumpers, instrument screens, small passenger and freight vehicles, as well as cab and machine covers for fire tanker trucks, refrigerated trucks, tractors, etc. 4. In terms of railway transportation, there are train window frames, curved roof panels, roof water tanks, water storage tanks, and certain railway communication facilities. 5. In terms of highway construction, there are traffic signs, isolation piers, signs, highway guardrails, and so on. 6. Inland passenger and cargo ships, fishing boats, hovercraft, high-speed boats, lifeboats, as well as fiberglass buoy drums and mooring buoys. 7. Electrical industry and communication engineering: including arc extinguishing equipment, cable protection tubes, generator stator coils and support rings and conical shells, insulation tubes, insulation rods, motor protection rings, etc
Link
Learn 2 new material
Lightweight and high-strength Corrosion resistanceGood electrical performance Good thermal performance Good designability Low elastic modulusPoor long-term temperature resistance Aging phenomenon Low shear strength
Use:
1. Construction industry: cooling towers, fiberglass building structures, indoor equipment and decorations, decorative panels, saunas, concrete formwork, reinforcement materials, and solar energy utilization devices. 2. Chemical industry: corrosion-resistant conveying pumps and their accessories, corrosion-resistant valves, ventilation facilities, wastewater treatment equipment, etc. 3. The automotive and railway transportation industry: automotive casings and other components, all plastic micro cars, bumpers, instrument screens, small passenger and freight vehicles, as well as cab and machine covers for fire tanker trucks, refrigerated trucks, tractors, etc. 4. In terms of railway transportation, there are train window frames, curved roof panels, roof water tanks, water storage tanks, and certain railway communication facilities. 5. In terms of highway construction, there are traffic signs, isolation piers, signs, highway guardrails, and so on. 6. Inland passenger and cargo ships, fishing boats, hovercraft, high-speed boats, lifeboats, as well as fiberglass buoy drums and mooring buoys. 7. Electrical industry and communication engineering: including arc extinguishing equipment, cable protection tubes, generator stator coils and support rings and conical shells, insulation tubes, insulation rods, motor protection rings, etc
Link
Learn 2 new material
Good thermal performance Good designability Low elastic modulusPoor long-term temperature resistance Aging phenomenon Low shear strength
Use:
1. Construction industry: cooling towers, fiberglass building structures, indoor equipment and decorations, decorative panels, saunas, concrete formwork, reinforcement materials, and solar energy utilization devices. 2. Chemical industry: corrosion-resistant conveying pumps and their accessories, corrosion-resistant valves, ventilation facilities, wastewater treatment equipment, etc. 3. The automotive and railway transportation industry: automotive casings and other components, all plastic micro cars, bumpers, instrument screens, small passenger and freight vehicles, as well as cab and machine covers for fire tanker trucks, refrigerated trucks, tractors, etc. 4. In terms of railway transportation, there are train window frames, curved roof panels, roof water tanks, water storage tanks, and certain railway communication facilities. 5. In terms of highway construction, there are traffic signs, isolation piers, signs, highway guardrails, and so on. 6. Inland passenger and cargo ships, fishing boats, hovercraft, high-speed boats, lifeboats, as well as fiberglass buoy drums and mooring buoys. 7. Electrical industry and communication engineering: including arc extinguishing equipment, cable protection tubes, generator stator coils and support rings and conical shells, insulation tubes, insulation rods, motor protection rings, etc
Link
Learn 2 new material
Low elastic modulusPoor long-term temperature resistance Aging phenomenon Low shear strength
Use:
1. Construction industry: cooling towers, fiberglass building structures, indoor equipment and decorations, decorative panels, saunas, concrete formwork, reinforcement materials, and solar energy utilization devices. 2. Chemical industry: corrosion-resistant conveying pumps and their accessories, corrosion-resistant valves, ventilation facilities, wastewater treatment equipment, etc. 3. The automotive and railway transportation industry: automotive casings and other components, all plastic micro cars, bumpers, instrument screens, small passenger and freight vehicles, as well as cab and machine covers for fire tanker trucks, refrigerated trucks, tractors, etc. 4. In terms of railway transportation, there are train window frames, curved roof panels, roof water tanks, water storage tanks, and certain railway communication facilities. 5. In terms of highway construction, there are traffic signs, isolation piers, signs, highway guardrails, and so on. 6. Inland passenger and cargo ships, fishing boats, hovercraft, high-speed boats, lifeboats, as well as fiberglass buoy drums and mooring buoys. 7. Electrical industry and communication engineering: including arc extinguishing equipment, cable protection tubes, generator stator coils and support rings and conical shells, insulation tubes, insulation rods, motor protection rings, etc
Link
Learn 2 new material
Aging phenomenon Low shear strength
Use:
1. Construction industry: cooling towers, fiberglass building structures, indoor equipment and decorations, decorative panels, saunas, concrete formwork, reinforcement materials, and solar energy utilization devices. 2. Chemical industry: corrosion-resistant conveying pumps and their accessories, corrosion-resistant valves, ventilation facilities, wastewater treatment equipment, etc. 3. The automotive and railway transportation industry: automotive casings and other components, all plastic micro cars, bumpers, instrument screens, small passenger and freight vehicles, as well as cab and machine covers for fire tanker trucks, refrigerated trucks, tractors, etc. 4. In terms of railway transportation, there are train window frames, curved roof panels, roof water tanks, water storage tanks, and certain railway communication facilities. 5. In terms of highway construction, there are traffic signs, isolation piers, signs, highway guardrails, and so on. 6. Inland passenger and cargo ships, fishing boats, hovercraft, high-speed boats, lifeboats, as well as fiberglass buoy drums and mooring buoys. 7. Electrical industry and communication engineering: including arc extinguishing equipment, cable protection tubes, generator stator coils and support rings and conical shells, insulation tubes, insulation rods, motor protection rings, etc
Link
Learn 2 new material
1. Construction industry: cooling towers, fiberglass building structures, indoor equipment and decorations, decorative panels, saunas, concrete formwork, reinforcement materials, and solar energy utilization devices. 2. Chemical industry: corrosion-resistant conveying pumps and their accessories, corrosion-resistant valves, ventilation facilities, wastewater treatment equipment, etc. 3. The automotive and railway transportation industry: automotive casings and other components, all plastic micro cars, bumpers, instrument screens, small passenger and freight vehicles, as well as cab and machine covers for fire tanker trucks, refrigerated trucks, tractors, etc. 4. In terms of railway transportation, there are train window frames, curved roof panels, roof water tanks, water storage tanks, and certain railway communication facilities. 5. In terms of highway construction, there are traffic signs, isolation piers, signs, highway guardrails, and so on. 6. Inland passenger and cargo ships, fishing boats, hovercraft, high-speed boats, lifeboats, as well as fiberglass buoy drums and mooring buoys. 7. Electrical industry and communication engineering: including arc extinguishing equipment, cable protection tubes, generator stator coils and support rings and conical shells, insulation tubes, insulation rods, motor protection rings, etc
Link
Learn 2 new material
3. The automotive and railway transportation industry: automotive casings and other components, all plastic micro cars, bumpers, instrument screens, small passenger and freight vehicles, as well as cab and machine covers for fire tanker trucks, refrigerated trucks, tractors, etc. 4. In terms of railway transportation, there are train window frames, curved roof panels, roof water tanks, water storage tanks, and certain railway communication facilities. 5. In terms of highway construction, there are traffic signs, isolation piers, signs, highway guardrails, and so on. 6. Inland passenger and cargo ships, fishing boats, hovercraft, high-speed boats, lifeboats, as well as fiberglass buoy drums and mooring buoys. 7. Electrical industry and communication engineering: including arc extinguishing equipment, cable protection tubes, generator stator coils and support rings and conical shells, insulation tubes, insulation rods, motor protection rings, etc
Link
Learn 2 new material
5. In terms of highway construction, there are traffic signs, isolation piers, signs, highway guardrails, and so on. 6. Inland passenger and cargo ships, fishing boats, hovercraft, high-speed boats, lifeboats, as well as fiberglass buoy drums and mooring buoys. 7. Electrical industry and communication engineering: including arc extinguishing equipment, cable protection tubes, generator stator coils and support rings and conical shells, insulation tubes, insulation rods, motor protection rings, etc
Link
Learn 2 new material
7. Electrical industry and communication engineering: including arc extinguishing equipment, cable protection tubes, generator stator coils and support rings and conical shells, insulation tubes, insulation rods, motor protection rings, etc
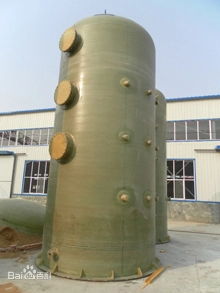
Learn 2 new material
Self-healing Polymer(SHP)
Self-healing polymers are a class of advanced materials that have the ability to self-repair cracks or damaged areas after damage, thereby extending the life of the material and improving its reliability and safety. This property mimics the self-healing mechanisms of certain organisms in nature and is an important innovation in materials science.
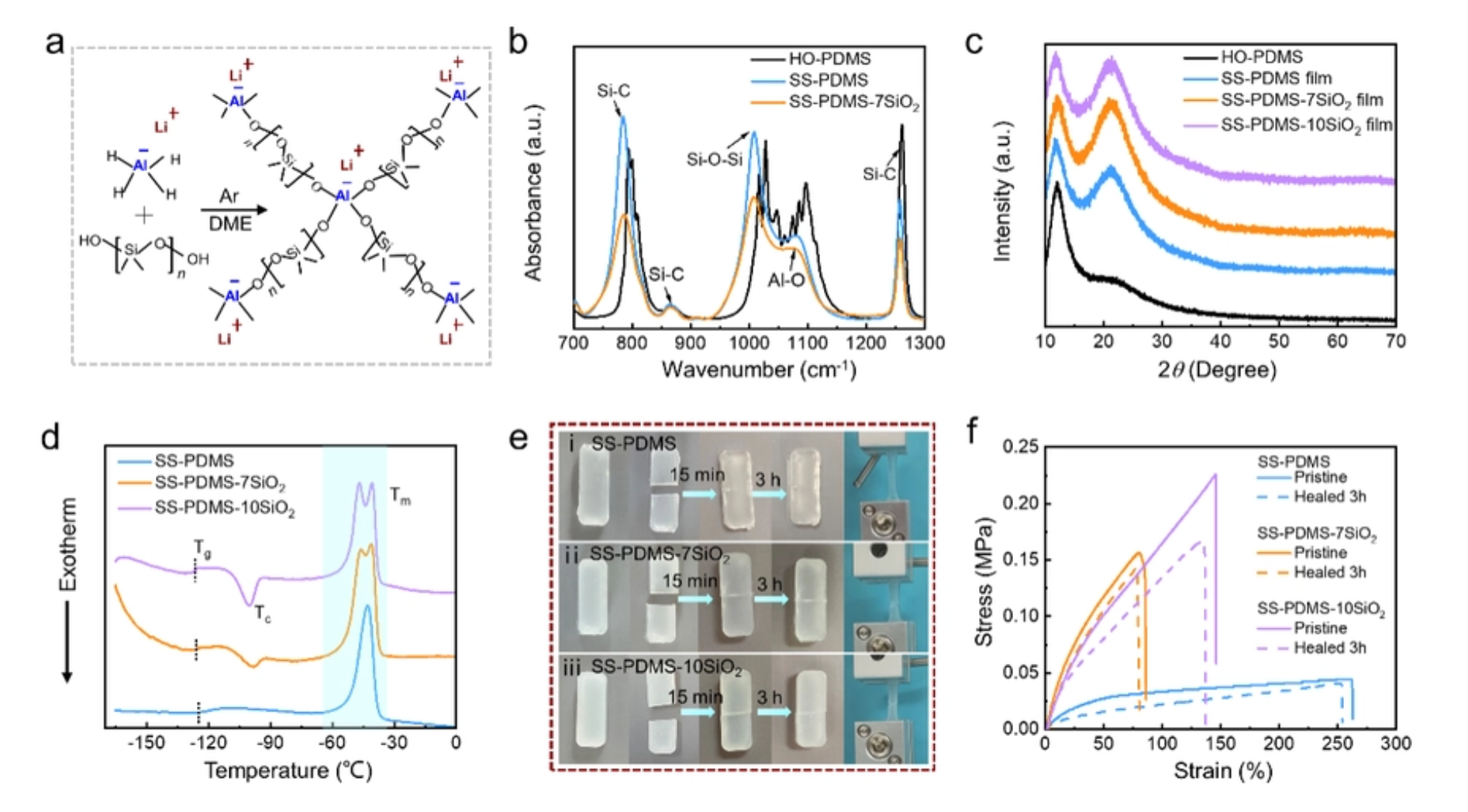
Features
a.Automatic repair ability: When the material is cracked or damaged due to external force, the self-healing polymer can automatically or under external stimulation to start the repair process without manual intervention.
b.Increased durability: With self-healing capabilities, these materials can significantly improve the overall durability and service life of the product. c.Wide range of applications: Self-healing polymers are used in many fields, including but not limited to aerospace, automotive manufacturing, building materials, electronic devices, biomedical implants and wearable devices. d.Design diversity: Self-healing mechanisms are diverse and can be realized based on dynamic covalent bond, non-covalent bond interaction, microencapsulation technology or enzymatic catalyzed reactions.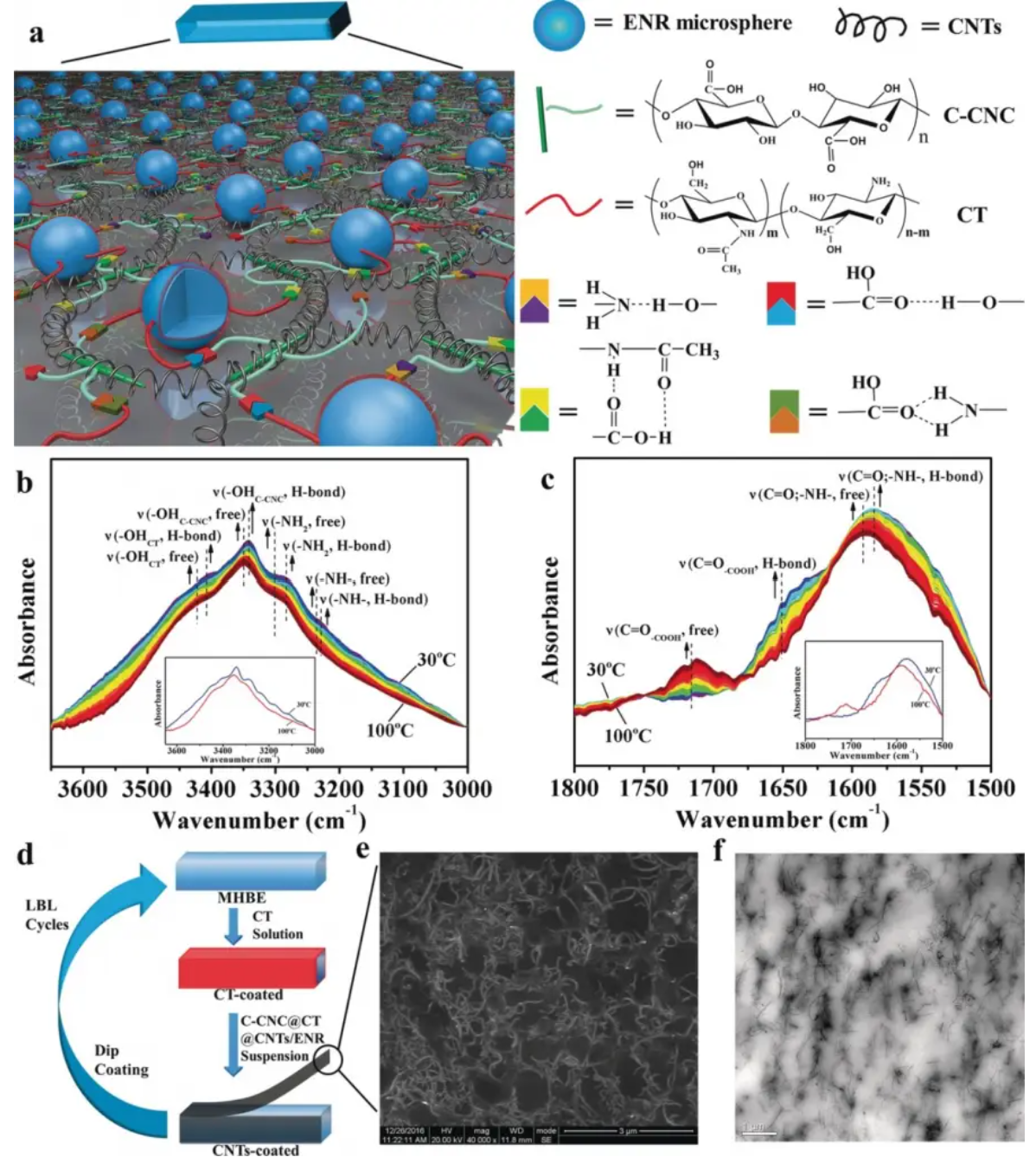
How it works
a.Microcapsule technology: Microcapsules containing restorants are embedded in a polymer matrix. When the material is damaged and the microcapsule breaks, a repair agent is released to fill the crack and re-form the chemical bond.
b.Vascular network system: A network of tiny channels is constructed inside the material, similar to the blood vessels of living organisms, through which repair fluid flows. When damage occurs, the repair fluid flows out and solidifies the crack. c.Dynamic chemical bonding: The use of chemical bonds with dynamic reversible properties (such as hydrogen bonds, metal coordination bonds, etc.) to join polymer chains. These bonds can be broken after damage and re-formed under the right conditions to achieve self-repair. d.Enzymatic reaction: When specific enzymes are added to the material, when the material is damaged, the enzyme is activated and catalyzes the repair reaction, promoting crack closure.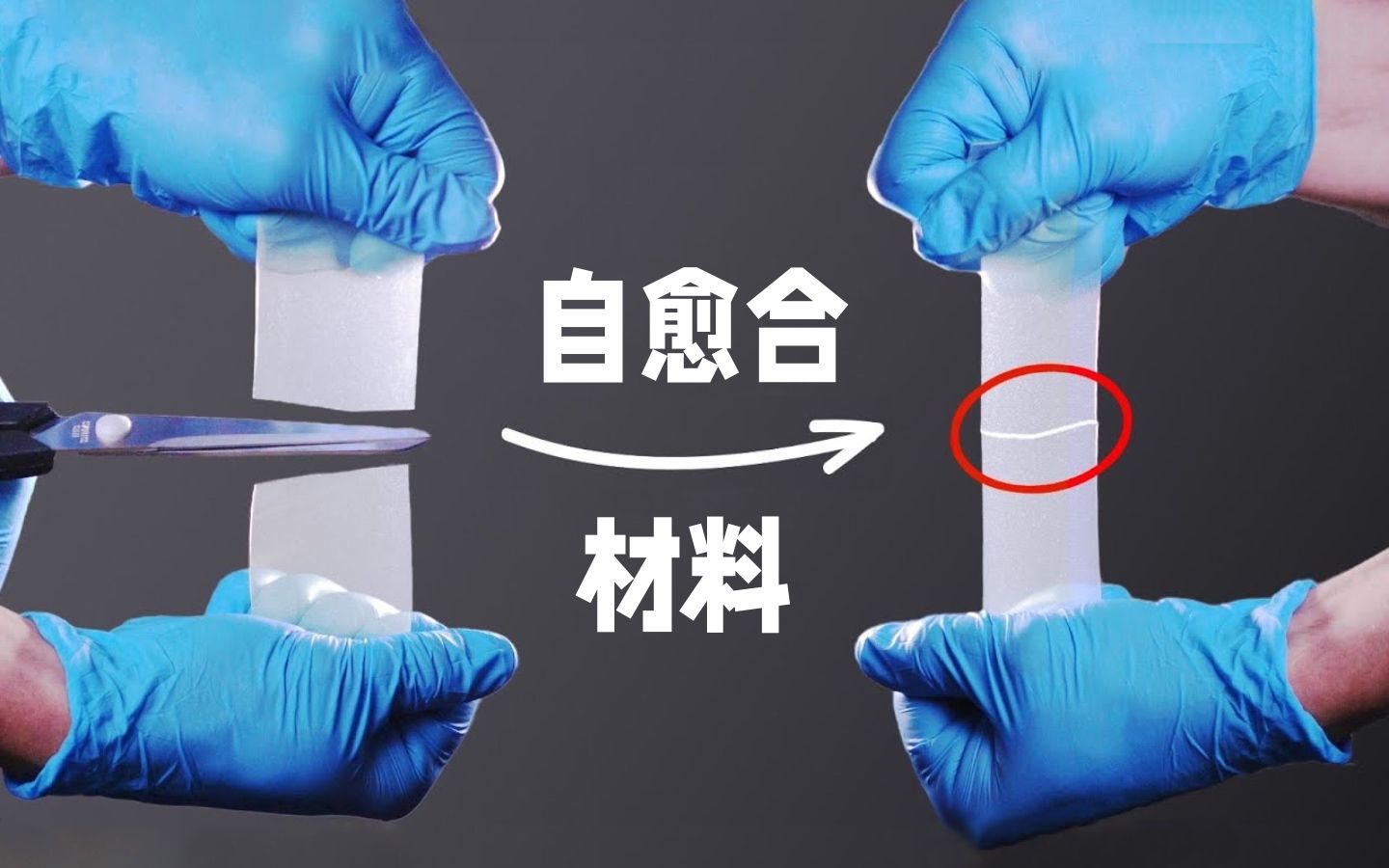
The latest developments
Researchers at the Indian Institute of Technology (IIT Bhilai) have developed a self-healing polymer coating material for photovoltaic applications that can self-heal cracks in minutes, providing a more durable protection solution for products such as solar panels. In addition, there are studies focused on improving the speed of self-healing, reducing costs, and developing more environmentally adaptable self-healing polymers, which are current research hotspots and challenges.
Quantum dot display materials
Quantum dot display materials are a revolutionary core component of display technology, based on the special optical properties of Quantum Dots (QDs). Quantum dots are nanoscale semiconductor crystals, usually around a few nanometers in size, that absorb light at one wavelength and emit light at another wavelength very efficiently due to quantum limiting effects, a property that allows quantum dots to produce extremely pure, highly saturated, monochromatic light.
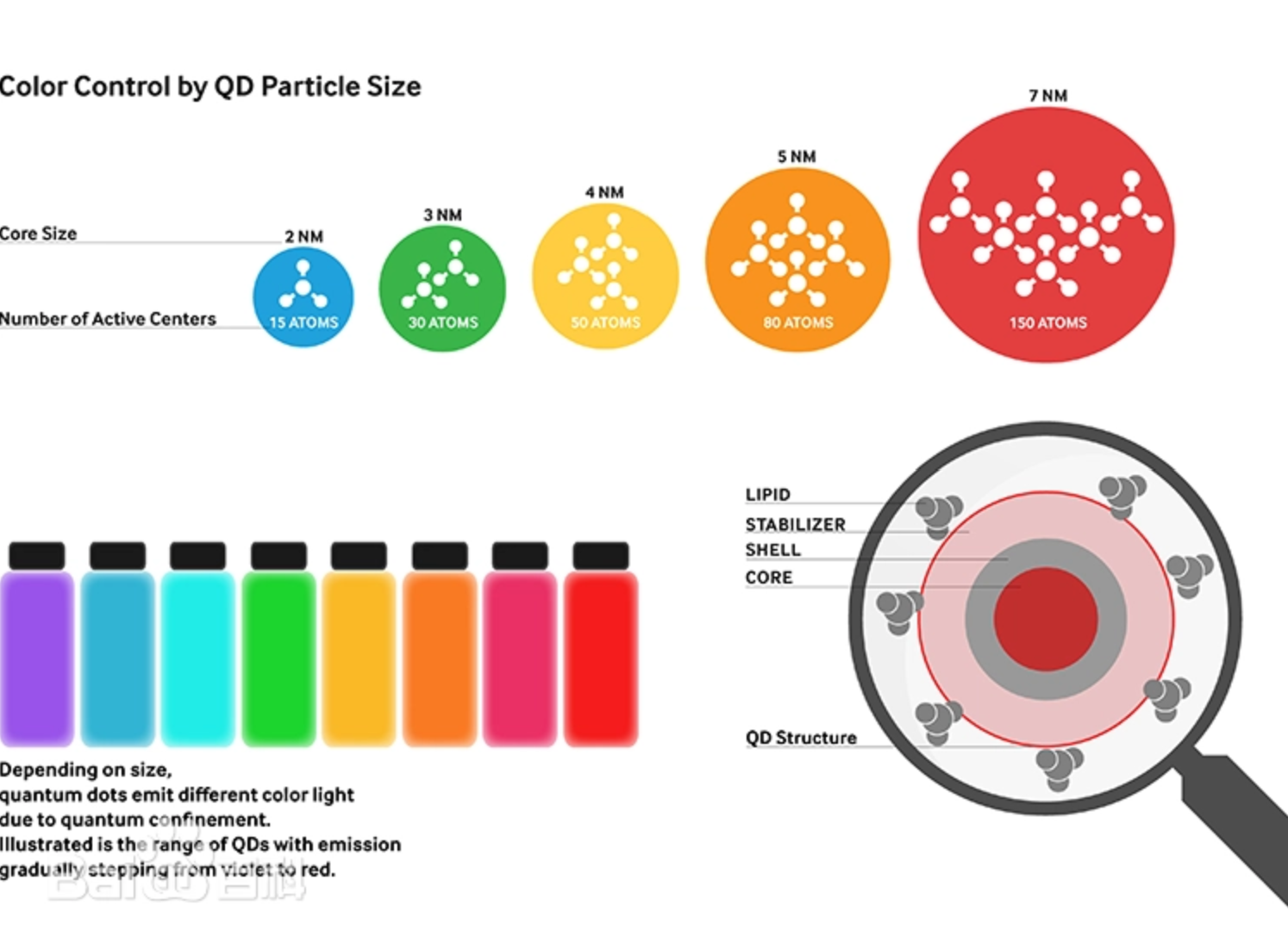
Features
a.Ultra-wide color gamut: Quantum dot display materials can significantly expand the color gamut coverage of a TV or monitor, and can provide more real-world color performance than traditional LCD or early OLED technology, especially in the red and green parts, making the image color more vivid and natural.
b.High energy efficiency: The conversion efficiency of quantum dot materials to light is extremely high, which means that at the same brightness, quantum dot display devices can be more energy-efficient than traditional display devices. c.Strong stability: Compared with some organic luminescent materials, quantum dots, as inorganic materials, have better light stability and thermal stability, which can ensure that the color is still bright after long-term use, extending the life of the display product. d.Thinness and flexibility: While current quantum-dot TVS are mainly based on LCD technology (QD-LCD), research is also advancing quantum-dot light-emitting diode (QLED) technology, which promises thinner panels and the possibility of flexible displays.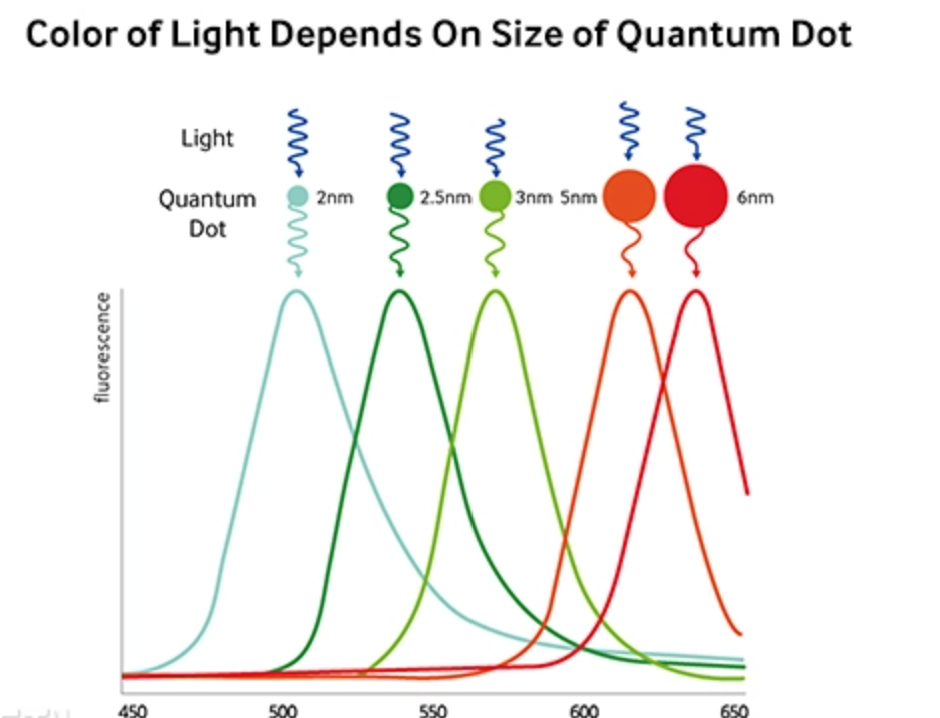
Application field:
a.Consumer Electronics: Quantum dot TVS are the most common application on the market today, providing a better picture quality experience than regular LCD TVS.
b.Future technology: With the advancement of QLED technology, quantum dot materials are expected to play an important role in emerging fields such as wearable devices, transparent displays, and even flexible displays. c.Professional display: In medical imaging, graphic design, film and television production and other industries, requiring highly accurate color reproduction scenes, quantum dot displays are also gradually favored.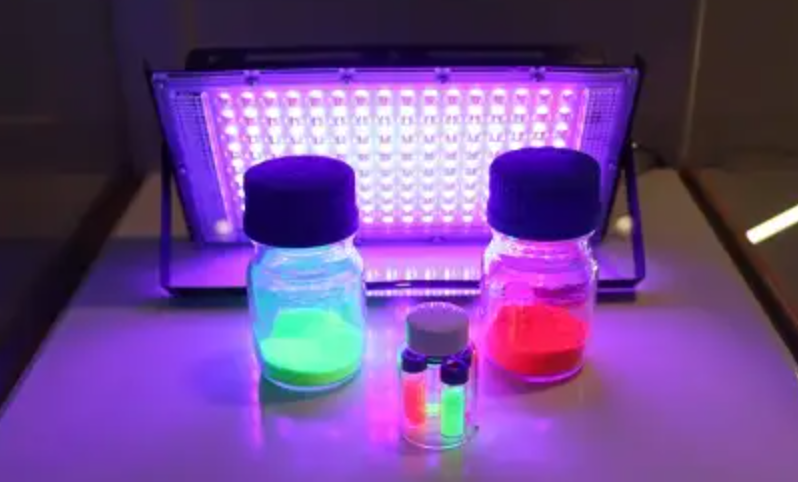
The latest developments
Although quantum dot display technology has gained a certain share in the market, researchers and companies continue to optimize the preparation process of quantum dots, explore more environmentally friendly quantum dot materials (reduce or avoid the use of harmful elements such as cadmium), and develop direct light emitting quantum dot display technology (QLED). The goal is to achieve lower power consumption, higher brightness and wider color gamut display effect, and further promote the innovation of display technology.
3. Find 1 methods post processing for 1 metal , 1 methods post processing for 1 plastic ,1 methods postprocessing for wood
1.Post-processing method of industrial pure iron
Heat treatment: annealing
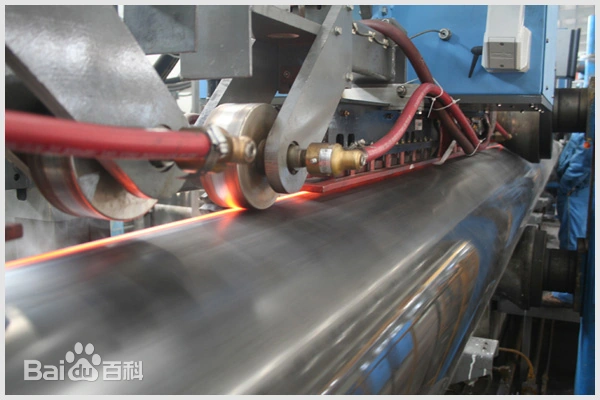
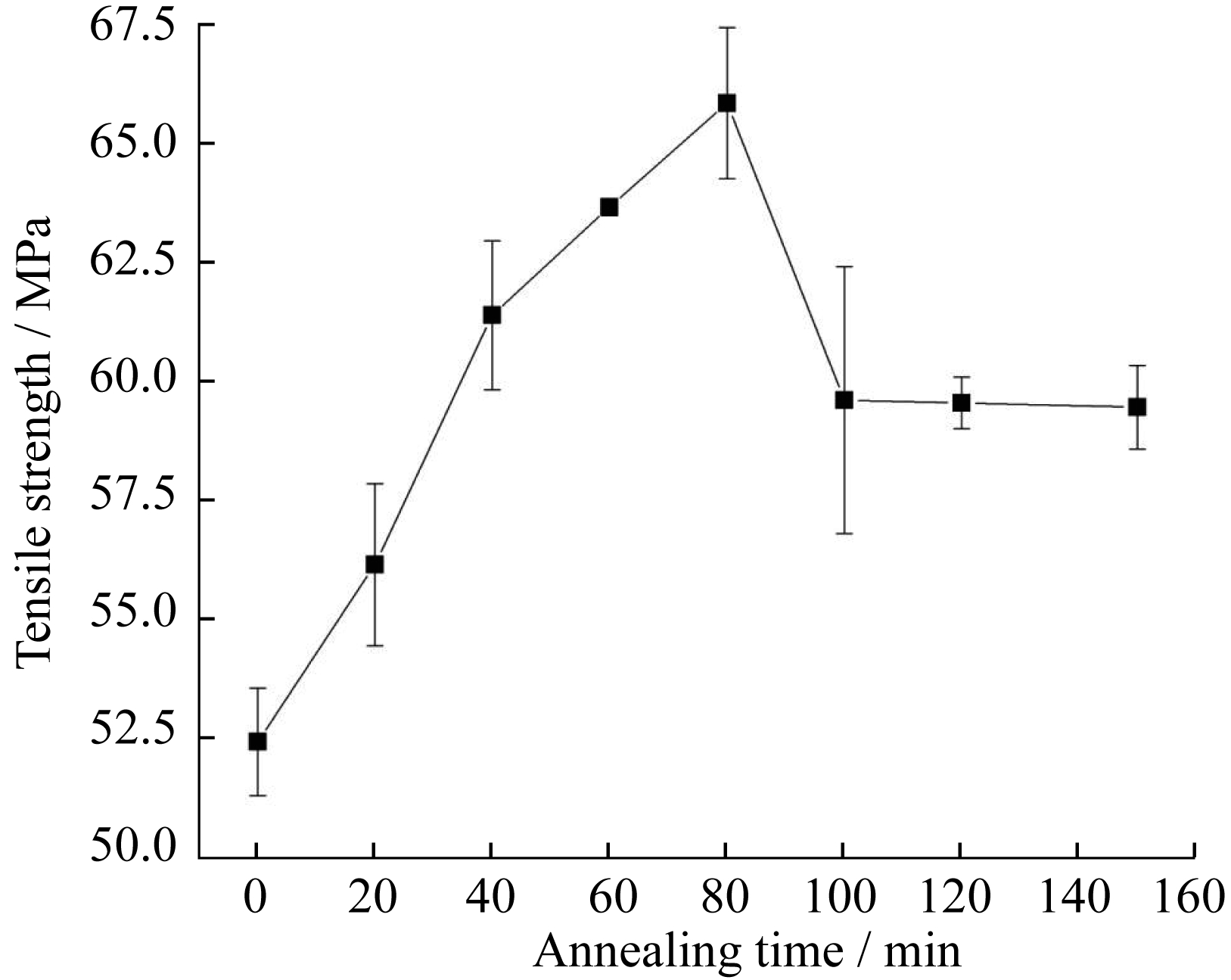
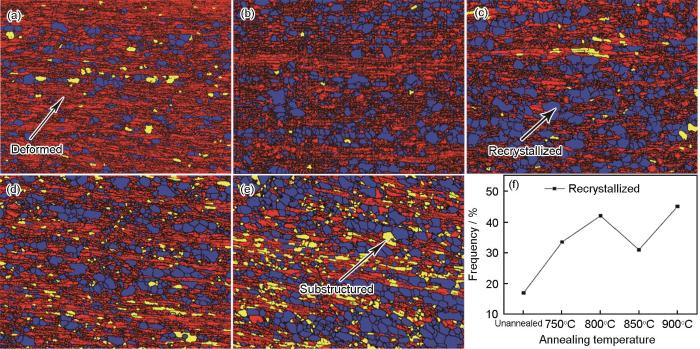
Annealing is a metal heat treatment process that refers to heating the metal slowly to a certain temperature, holding it for a sufficient period of time, and then cooling it at a suitable rate. Function: (1). Reduce hardness and improve cutting and machinability;
(2) Reduce residual stress, stabilise the size, reduce deformation and cracking tendency; (3) refine the grain, adjust the organisation, eliminate organisational defects: the metal is composed of a lot of very small "grains", if the grain is too large or unevenly distributed, the performance of the metal will be affected. Annealing can make these grains smaller and more evenly distributed, as if rearranging the internal structure of the metal to make it more perfect, which can eliminate some of the defects that lead to uneven metal properties. (4) Uniform material organisation and composition, improve material properties or prepare the organisation for later heat treatment.2.Post-processing method of PE
Polyethylene (PE) cross-linking technology
After cross-linking modified PE can make its performance has been greatly improved, not only significantly improve the PE mechanical properties, environmental stress cracking resistance, chemical resistance, corrosion resistance, creep resistance and electrical properties and other comprehensive performance, but also very obviously improve the temperature resistance level, can make the PE heat-resistant temperature from 70 ℃ to more than 100 ℃, thus greatly broadening the application areas of PE.
Chemical cross-linking: Silane cross-linking and cross-linking agent
This technology uses vinyl silane containing double bonds to react with molten polymers under the action of an initiator to form a silane-grafted polymer, which is hydrolysed in contact with water in the presence of a silanol condensation catalyst to form a reticulated oxyalkane-chained cross-linking structure. Silane cross-linking technology due to its cross-linking equipment used is simple, the process is easy to control, less investment, high degree of cross-linking of the finished product, good quality, thus greatly promoting the production and application of cross-linked polyethylene. In addition to polyethylene, silane, crosslinking also need to use catalysts, initiators, antioxidants and so on.
3.Post-processing method of wood
Paint treatment
Link
Paint treatment, Paint treatment is a common surface treatment for wood. It protects the wood from moisture, corrosion and other factors and extends the life of the wood. Paint treatment can be chosen in different colours and sheens to make the wood surface look more beautiful. Painting is divided into the following steps:
1. cleaning the wood surface
2. trimming and sanding 3. filling holes and cracks 4. applying paint 5. coating: after the first coat dries, a second coat is applied to increase coverage and durability. 6. drying 7. sanding and polishing 8. protective coatings
Introduce detail all materails in your final project
1.pla 3d printing material makes consumables for hose 3d printing
2.pvc hose is used to guide liquid flow
3.pet plastic bottles or glass bottles are collected for liquid testing
4.The use of acrylic plate for the production of the shell has been fixed components
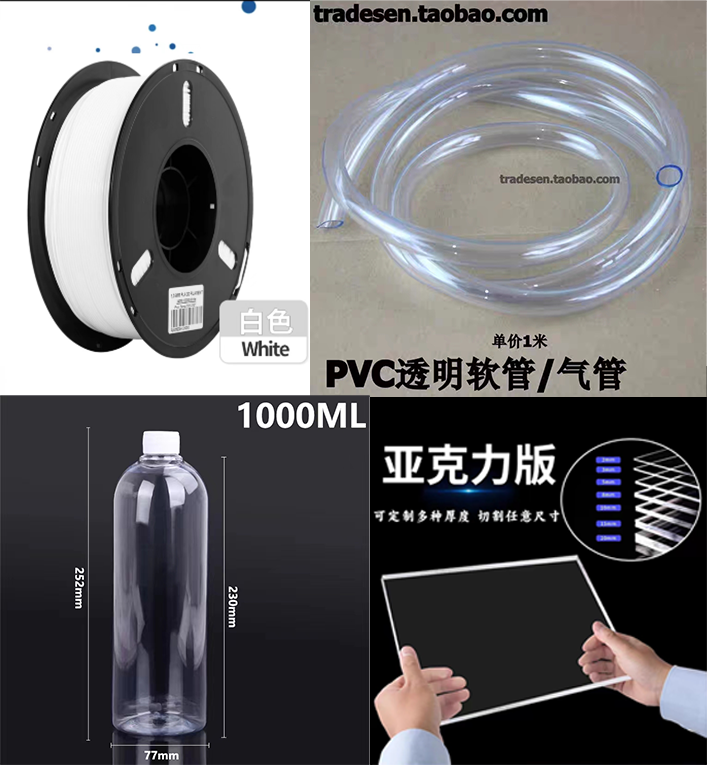