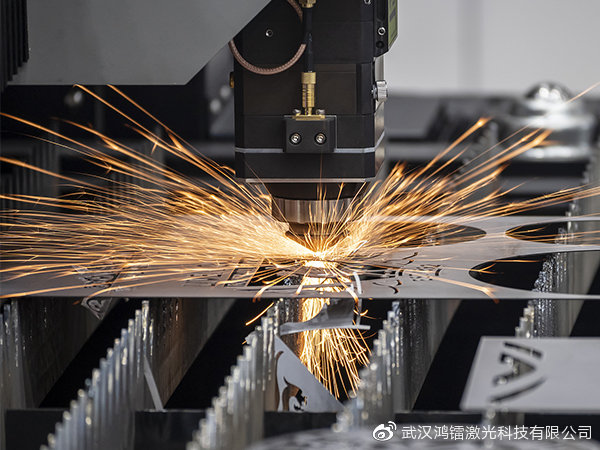
How to ensure safety ?
Wear personal protective equipment:
Operators must wear appropriate personal protective equipment, such as laser safety glasses or face shields, to ensure that their eyes and skin are not damaged by laser radiation.
Corresponding wavelength: 1064/405nm
Equipment maintenance and calibration:
Ensure that laser cutting equipment is regularly maintained and calibrated to ensure that it operates within safe parameter ranges.



Work Area Restrictions:
Use safety barriers or other appropriate facilities to restrict unauthorized personnel from entering the work area and prevent unintentional exposure to laser radiation.
Emergency stop and emergency plan:
Design and implement emergency stop buttons and prepare emergency plans to respond to unexpected events such as laser leakage or equipment failure.
Ventilation and protective measures:
Ensure sufficient ventilation in the work area to prevent the impact of smoke, dust, and gases generated during laser cutting on operators.
Laser cutting materials
Stainless Steel
The advantages of stainless steel as a laser cutting material:
1.High precision
Laser cutting of stainless steel pipes is a high-precision processing method, with an accuracy of less than 0.1mm. This high-precision machining can not only meet the high precision requirements of component processing in industrial production, but also meet the needs of art, model making and other fields.
2.High efficiency
Compared to traditional processing methods, laser cutting of stainless steel pipes has higher processing efficiency. On the one hand, laser cutting equipment is easy to operate and can complete complex shape cutting in a short time; On the other hand, the power density of lasers is high, and high-power lasers can be used to cut stainless steel pipes of different thicknesses, greatly shortening the processing cycle and improving production efficiency.
3.Security
In the process of laser cutting, there is no need to fix the material, and there are no issues such as vibration and noise, avoiding safety hazards caused by vibration or noise in traditional processing.
Brands suitable for laser cutting
1. # 304 grade stainless steel
2. # 201 grade stainless steel
3. # Q235 grade stainless steel
4. # Q345 grade stainless steel
Ensuring CNC security
Training and Education:
All operators should receive professional training to understand the operating procedures, safety precautions, and emergency response methods of CNC machine tools.
Programming and operating standards:
Strictly adhere to programming and operating standards to avoid accidents caused by operational errors or incorrect program settings. Ensure that each step of the operation follows the correct procedures and standards.
Operation monitoring and tracking:
Real time monitoring and tracking of CNC machine operation is carried out through the monitoring system, and abnormal situations are detected in a timely manner and measures are taken.
Introduction to CNC process
CO2 laser cutting
Working principle:
Using CO2 gas as the excitation medium, laser amplification occurs, and cutting is carried out after focusing through an optical system.
Applicable materials:
Suitable for both metal and non-metal materials, such as stainless steel, aluminum alloy, wood, plastic, etc.
Application scenarios:
Widely used in metal processing (such as automotive parts, household appliances, aerospace), cutting of non-metallic materials (such as paper, fabric, leather, etc.), and process processing (such as carving, punching, etc.).
Fiber laser cutting
Working principle:
Using fiber optic as the laser medium, the laser beam is transmitted through the fiber optic and cut through a focusing optical system.
Applicable materials:
mainly used for metal materials, such as stainless steel, aluminum alloy, carbon steel, etc.
Application scenarios:
Especially suitable for applications that require high-speed and high-precision cutting, such as automotive manufacturing, aerospace, electronic equipment production, etc.
Confirm the equipment and materials used for the application
Equipment:
CNC Milling Machine:
Equipment used for cutting, cutting, or engraving operations on workpieces. Suitable for processing materials such as metal, plastic, wood, etc.
CNC Lathe Machine:
a device used to rotate workpieces and perform precise cutting or trimming. Mainly suitable for metal processing, such as steel, aluminum, etc.
CNC Laser Cutting Machine:
a device that uses laser beams for high-precision and high-speed cutting. Suitable for processing metal and non-metallic materials, such as steel, aluminum, wood, leather, etc.
CNC Punching Machine:
Equipment used for stamping, punching, or forming flat materials. Suitable for processing metal sheets, such as steel plates.
Material Science:
Metal materials:
including steel, stainless steel, aluminum, copper and other metal materials, suitable for various processing operations.
Plastic materials:
such as polyvinyl chloride (PVC), polypropylene (PP), polystyrene (PS), etc., suitable for cutting, carving, forming and other processing.
Wood materials:
such as plywood, density board, solid wood, etc., suitable for cutting, carving, hollowing and other processing.
Composite materials:
such as carbon fiber composite materials (CFRP), glass fiber composite materials (GFRP), etc., suitable for cutting, drilling and other processing.
For example
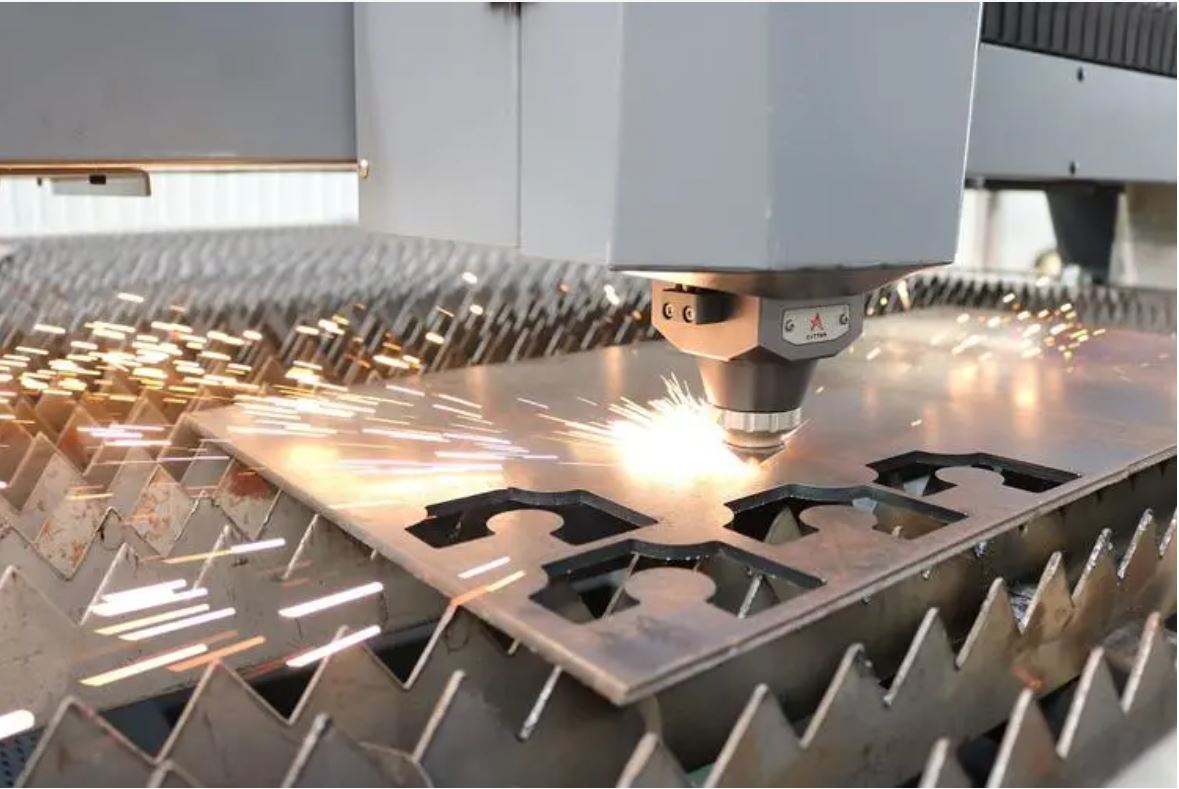
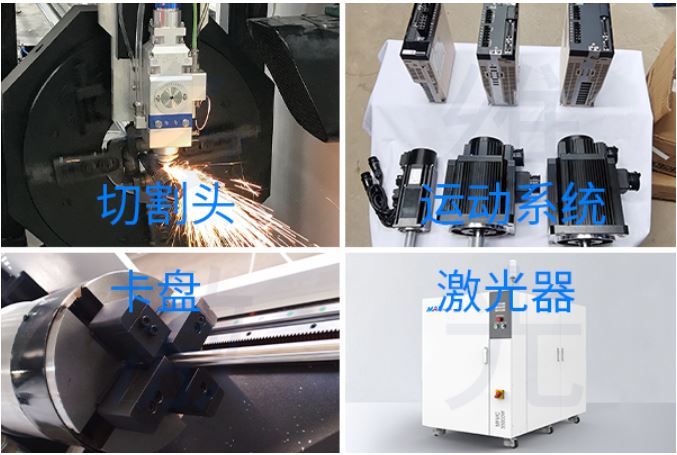
Metal laser cutting machine
Application: Used in various manufacturing and processing industries such as sheet metal processing, aviation, aerospace, electronics, electrical appliances, subway accessories, automobiles, machinery, precision accessories, ships, metallurgical equipment, elevators, household appliances, craft gifts, tool processing, decoration, advertising, and metal external processing.
Mainly used for rapid cutting of various metal materials such as carbon steel, silicon steel, stainless steel, aluminum alloy, titanium alloy, galvanized sheet, pickled sheet, aluminum zinc plated sheet, copper, etc.
The process of laser cutting
1、 Preparation work
1. Check the equipment: Ensure that the laser cutting machine is in normal working condition, and check whether the power supply, air source, water cooling system, etc. are connected properly.
2. Prepare the workpiece: Place the workpiece to be cut on the workbench and secure it to ensure that it is flat and stable.
3. Personal safety: Wear protective equipment, including goggles, gloves, etc,
2、 Adjusting cutting parameter
1. Select cutting material type: Set the cutting parameters of the laser cutting machine, such as power, speed, etc., based on the material of the workpiece.
2. Adjust cutting focal length: Adjust the cutting focal length of the laser cutting machine according to the thickness of the workpiece, ensuring that the laser beam can be accurately focused on the workpiece
surface
3. Set cutting path: Based on the shape of the workpiece and the contour to be cut, set the cutting path, which can be assisted by laser cutting software
3、 Start cutting
1. Start the equipment: Turn on the power of the laser cutting machine and start the equipment according to the requirements of the equipment manual.
2. One click autofocus: Some laser cutting machines are equipped with autofocus function, which can achieve fast and accurate focal length through one click operation
adjustment
3. Manual focusing: If the laser cutting machine does not have an automatic focusing function, manually adjust the cutting focal length to ensure that the laser beam is focused on the surface of the workpiece
4. Start cutting: Press the start button to start the cutting process of the laser cutting machine, pay attention to the situation during the cutting process, and ensure the cutting quality
4、 Post cutting treatment
1. Stop cutting: When the cutting is completed and needs to be paused, press the stop button to stop the cutting operation of the laser cutting machine.
2. Post treatment: Clean and polish the cut workpiece as needed to achieve better cutting effect and surface quality
3. Turn off the device: Turn off the power of the laser cutting machine, pay attention to safety, and avoid accidental contact.
Back